BLOG
Field Robot Docking Station: How to Ensure -20 °C to +50 °C Reliability for Agricultural Robots
Table of contents
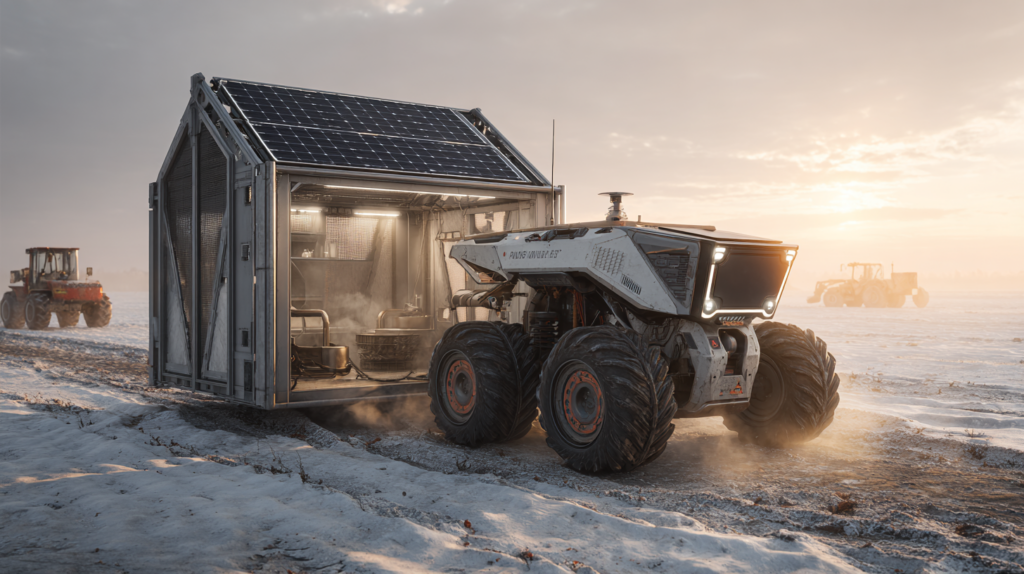
Agricultural robots are transforming how modern farms operate, handling everything from crop monitoring and spraying to soil sampling and harvest support. But these machines don’t just work in greenhouses or fair-weather fields—they must operate through frosty mornings and sweltering afternoons. The success of any field robot depends on one essential but often overlooked component: a rugged, temperature-resilient docking station. Without reliable charging and sheltering systems, even the most advanced robot is just a high-tech scarecrow.
To support true field autonomy, the docking station must be engineered for extreme environmental fluctuations, offering consistent operation from -20 °C during cold dawns to +50 °C under the summer sun. This article explores how to design and deploy docking stations that meet this challenge, providing the dependable uptime agricultural robotics require.
Why Extreme Temperature Reliability Matters for Agricultural Robotics
Agricultural robots operate in some of the harshest environments, and their performance hinges on uninterrupted power and reliable communication. Docking stations that falter during temperature spikes or drops can stall operations and create maintenance headaches.
Top Features
- Ruggedized enclosures with high IP ratings for dust, humidity, and heat resistance
- Integrated battery heating elements and ventilation fans
- Redundant temperature sensors to monitor internal thermal conditions
- Wide-temperature-rated connectors, cables, and housing materials
Top Benefits
- Prevents battery degradation due to thermal stress
- Minimizes downtime from cold-start issues or overheating failures
- Enables true 24/7 autonomous robot operation
- Reduces the need for human intervention in remote fields
Best Practices
- Use PCBs rated for -40 °C to +85 °C to exceed minimum temperature needs
- Select polycarbonate or powder-coated metal enclosures for UV and heat resistance
- Install backup heating systems for overnight frost protection
- Integrate data logging for real-time thermal analytics
By prioritizing extreme temperature reliability from the start, engineers can avoid costly field failures and boost long-term deployment success.
Choosing the Right Materials for Harsh Environmental Performance
Material selection plays a crucial role in ensuring docking station resilience. Subpar plastics or metal alloys may warp, crack, or degrade in fluctuating temperatures or under prolonged sun exposure.
Top Features
- UV-stabilized polycarbonate housings
- Aluminum alloys with powder coating for corrosion resistance
- Silicone gaskets and thermal seals rated for industrial outdoor use
- Conformal coating on PCBs to protect against condensation and corrosion
Top Benefits
- Withstands agricultural chemicals, dust, and sun exposure
- Prevents seal failure during freeze-thaw cycles
- Maintains mechanical strength even in prolonged heat
- Ensures long lifecycle even under daily exposure to water and debris
Best Practices
- Avoid ABS or basic PVC housings for outdoor stations—opt for industrial polymers
- Apply thermal paste or insulating pads around key PCB components
- Perform salt spray and UV testing to verify long-term resistance
- Design mechanical structures to allow for thermal expansion without cracking
Durable, properly tested materials ensure that docking stations maintain full functionality year-round, even in the most unforgiving climates.
Thermal Management Systems for Docking Stations
Effective thermal management ensures internal electronics remain within safe operating limits, even when the external environment pushes extremes. This is essential for both robot safety and charging performance.
Top Features
- Thermostatically controlled fans and heaters
- Heat sinks and internal airflow channels
- Ventilation filters that block dust and debris
- Smart thermostat ICs that adjust thermal profiles dynamically
Top Benefits
- Protects battery management systems (BMS) from overheating or freezing
- Extends the life of power electronics and chargers
- Allows precise temperature control for charging optimization
- Reduces risk of condensation inside enclosures
Best Practices
- Place heaters near battery contacts and power modules
- Use PTFE-coated filters to maintain ventilation without letting in particles
- Monitor internal humidity along with temperature for full climate control
- Test thermal cycles across -20 °C to +50 °C to simulate real-world usage
Thermal control isn’t just about comfort—it’s mission-critical to robot uptime and operational safety.
CLIENT'S QUOTE
"Phihong’s PoE solutions have made a huge difference for us! Our network runs more efficiently, and we’ve seen real cost savings. We couldn’t be happier!"
Power Supply Design for Temperature-Extreme Environments
Even the best docking station fails if its internal power supply can’t deliver steady current in the cold or heat. Power components must be derated and tested under temperature duress.
Top Features
- Wide operating range AC-DC or DC-DC converters (-40 °C to +85 °C)
- Over-voltage and under-voltage protection in fluctuating supply environments
- Conformal-coated power modules with EMI shielding
- GaN or SiC-based switching components for thermal efficiency
Top Benefits
- Ensures fast, consistent charging regardless of weather
- Prevents power module failure during field voltage irregularities
- Boosts energy efficiency even under full thermal load
- Reduces power loss and heat buildup during continuous charging
Best Practices
- Derate power supply output current by 20–30% at maximum temperatures
- Test power modules with field-ready load simulators under extreme heat/cold
- Use ferrite core inductors to reduce EMI at high temps
- Install surge protection for lighting and electrical instability protection
Phihong’s high-performance power modules are designed specifically for rugged applications like this—perfect for field robot docking platforms.
Integrating Smart Sensors and Communication in All Weather Conditions
For remote diagnostics and predictive maintenance, sensors and communication modules must stay active regardless of environmental changes. Failure in communication can halt entire fleets.
Top Features
- Wide-temp-rated CANBus and RS-485 transceivers
- Weatherproof antenna ports with 4G/5G/Wi-Fi fallback
- IP-rated sensor housings with internal thermal isolation
- Redundant data logging and remote sync capabilities
Top Benefits
- Provides real-time robot status to the control center
- Supports AI-powered predictive maintenance models
- Reduces travel time for field technicians
- Enables over-the-air firmware and performance updates
Best Practices
- Use cellular modules with eSIM support for global deployment
- Validate sensor readings under thermal stress to eliminate false triggers
- Log charging patterns to detect performance drops due to temperature
- Shield antennas from snow, sun, and impact using molded housing
Robust communication design ensures that your robot docking infrastructure stays connected—no matter the conditions.
Installation and Maintenance Best Practices for Year-Round Operation
Designing a great docking station is only half the job—ensuring it performs 365 days a year requires strategic deployment and scheduled upkeep.
Top Features
- Mounting anchors for snow and wind resistance
- Drainage systems to prevent water accumulation
- Modular internal compartments for fast servicing
- RFID or QR scan access panels for technician workflows
Top Benefits
- Reduces damage risk from storms, tractors, or animals
- Makes maintenance faster and cheaper with quick-swap parts
- Ensures safety for on-site teams during servicing
- Allows scalable fleet management across vast farms
Best Practices
- Mount stations above ground level to avoid puddle corrosion
- Train farm staff on seasonal checks and firmware updates
- Deploy in shaded or semi-covered areas to reduce direct sun exposure
- Use mobile dashboards to track thermal and power metrics over time
Good installation equals long-term ROI. Agricultural docking stations must be more than rugged—they must be serviceable, scalable, and smart.
How Phihong USA Helps You Build Reliable Docking Stations for Agricultural Robots
Phihong USA specializes in power solutions engineered for challenging environments—including extreme temperature operation. Whether you’re designing modular field robot docking shelters or rugged outdoor charging enclosures, our wide-temperature-rated power supplies, weatherproof enclosures, and intelligent thermal control systems are designed to meet industrial-grade reliability standards.
From high-efficiency GaN-based DC chargers to waterproof connectors and BMS integration modules, Phihong’s portfolio empowers OEMs and system integrators to go from prototype to production with confidence.
Looking to future-proof your agricultural robot deployments? Contact Phihong today to explore how we can help you design smarter, more resilient docking systems. Email: usasales@phihongusa.com
Contact Our Team Today!
Our dedicated sales team and international partners are prepared to support you with your latest projects and initiatives globally.
Explore More with Phihong USA
As we conclude our exploration of PoE technology, it’s evident how these innovations are streamlining power and data integration across various industries. Phihong USA stands at the forefront of this technological advancement, offering a diverse range of power solutions designed to meet the evolving needs of modern industries.
Phihong USA’s extensive product lineup includes:
- Power over Ethernet (PoE) Solutions: Delivering reliable power and data transmission over a single cable, ideal for simplifying network installations and reducing costs.
- AC/DC Adapters and Power Supplies: From compact adapters to industrial-grade power supplies, Phihong provides solutions that ensure efficiency and reliability in various applications.
- Battery Chargers: Customizable chargers for lithium-ion and lead-acid batteries, supporting a wide range of power requirements for mobility and industrial applications.
- Medical Power Supplies: Specialized power solutions designed to meet the stringent requirements of the healthcare industry, ensuring safety and reliability.
Phihong USA is committed to innovation and excellence, continually developing products that meet the highest standards of performance and reliability. Their global reach and dedication to customer support make them a trusted partner in powering the future.
Here are some useful links to explore Phihong USA’s offerings further and bring in new potential clients:
Visit Phihong USA to discover how their advanced power solutions can support your business needs. Whether you’re looking to upgrade your network, or find reliable power supplies, Phihong USA has you covered.
By choosing Phihong USA, you’re partnering with a leader in power technology, ensuring your operations run smoothly and efficiently with top-tier power solutions. Contact Us today!
FAQ
What temperature range should a field robot docking station support?
A reliable agricultural robot docking station should support a temperature range from at least -20 °C to +50 °C. This range ensures proper functionality in freezing mornings, hot summer afternoons, and sudden temperature swings. If you’re operating in areas with more severe winters or direct sun exposure, it’s even better to design for -30 °C to +60 °C. Inside the dock, power electronics, battery packs, and PCBs need to remain operational. This often requires internal thermal control systems—like heaters, fans, or even active cooling in rare cases. Engineers should also test for condensation, thermal cycling, and UV degradation to ensure year-round stability.
How do docking stations prevent overheating or freezing?
Docking stations integrate thermal regulation systems to manage temperature extremes. These may include passive techniques like insulation and reflective coatings, or active systems such as thermostatically controlled fans and internal heating elements. Heaters prevent battery and PCB freezing during winter operations, while exhaust fans or heat sinks dissipate excess heat during peak sun exposure. Thermal sensors continuously monitor internal conditions, and the system can trigger alerts or halt charging to avoid damage. For best results, it’s common to deploy smart climate control mechanisms that adjust behavior based on both internal and external temperatures.
What are the best materials for outdoor robot docking stations?
The best materials for year-round outdoor use are those that withstand UV radiation, moisture, thermal expansion, and chemical exposure. UV-stabilized polycarbonate, powder-coated aluminum, and stainless steel are excellent choices. Seals should be made of silicone or EPDM rubber, and fasteners should be stainless or corrosion-resistant alloys. Internally, PCBs should be conformal coated to resist condensation and debris. Using IP65 or higher-rated enclosures is critical. Avoid low-grade ABS or untreated plastics, which can warp or crack. Material selection should also factor in farm chemical exposure, including fertilizers and pesticides.
Can Phihong power modules operate reliably in extreme climates?
Yes. Phihong offers a wide portfolio of power modules rated from -40 °C to +85 °C, far exceeding most outdoor application needs. These modules are used in industrial, military, and agricultural environments where heat and cold are constant challenges. Phihong’s AC-DC and DC-DC converters come with built-in protections for over-voltage, under-voltage, thermal shutdown, and EMI shielding. Our power supply units are designed with long-life electrolytic capacitors and high-efficiency switching to minimize heat buildup. These features make Phihong an ideal partner for outdoor robotics, autonomous systems, and ruggedized equipment needs.
How often should agricultural robot docking stations be maintained?
Docking stations should undergo quarterly inspections, especially in regions with wide seasonal temperature swings. Maintenance includes checking seals, power connections, battery performance, thermal sensors, and physical enclosure integrity. In winter, heater systems and cold-start behavior should be validated. In summer, fans and ventilation should be inspected for blockages. Firmware should be updated regularly to maintain sensor calibration and communication stability. Many modern systems also support remote diagnostics, which allow predictive maintenance and reduce the need for field visits. Following a seasonal checklist can extend the life and performance of your station dramatically.