BLOG
Medical Power Supply Manufacturer: How to Meet IEC 60601‑1 When Manufacturing Medical Power Supplies
Table of contents
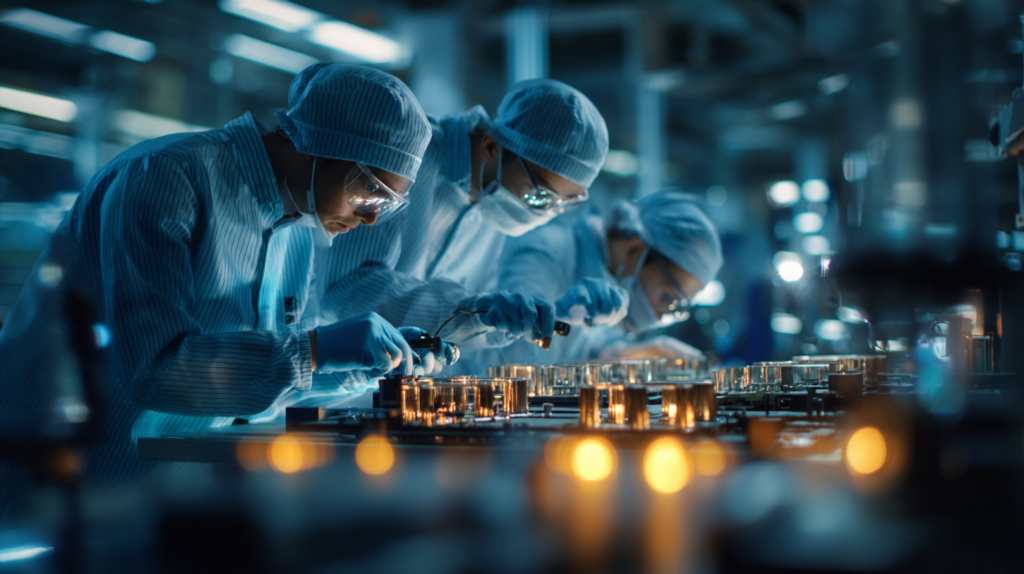
What Is IEC 60601‑1 and Why Is It Critical in Medical Power Supply Manufacturing?
IEC 60601‑1 is the international standard that governs the safety and performance of electrical medical equipment. For OEMs manufacturing medical power supplies, this standard is not optional—it’s mandatory for market access in nearly every global healthcare setting. Whether you’re powering patient monitoring devices, surgical systems, or home-use medical equipment, compliance with IEC 60601‑1 ensures the safety of both patients and operators.
The standard covers a wide range of safety criteria, including:
- Electrical shock protection
- Fire and mechanical hazard mitigation
- EMI (electromagnetic interference) and EMC (compatibility)
- Isolation between patient-touching and energy-carrying components
IEC 60601‑1 compliance also includes risk management protocols aligned with ISO 14971. That means manufacturers must not only design safe products but also document every potential failure mode and mitigation strategy.
Top Features
- 2 x MOPP (Means of Patient Protection) isolation compliance
- Low leakage current design for patient-contact systems
- Reinforced insulation and protective earth paths for operator safety
Top Benefits
- Enables global market approval and regulatory acceptance
- Reduces risk of product recalls or liability claims
- Builds trust with hospitals, clinics, and device OEMs
Best Practices
- Engage with a power supply manufacturer experienced in IEC 60601‑1
- Validate both component-level and system-level compliance early
- Maintain complete traceability and risk documentation from prototype to production
IEC 60601‑1 compliance isn’t just technical—it’s a foundation of credibility and patient safety in medical device design.
What Are the Key Electrical Safety Requirements in IEC 60601‑1?
Electrical safety is a core pillar of IEC 60601‑1. Power supplies used in medical equipment must be engineered to protect both the patient and the operator—even in fault conditions. That means robust isolation, controlled leakage current, and fault-tolerant design are not just features—they’re requirements.
The standard defines multiple protection mechanisms:
- Means of Operator Protection (MOOP) and Means of Patient Protection (MOPP), with 2 x MOPP being the strictest classification
- Creepage and clearance distances to prevent arcing or component breakdown
- Touch current limits, particularly important in patient-connected devices
Power supplies must also comply with low-voltage directive standards and harmonized EMC regulations. For patient-connected equipment (Type BF or CF), even microamps of leakage can be unacceptable.
Top Features
- Low leakage current (<100 µA for CF-rated supplies)
- Reinforced insulation and double-fused inputs
- Fail-safe design with overload and short-circuit protection
Top Benefits
- Prevents electrical shock and medical device failure
- Ensures compatibility with global safety audits and hospital requirements
- Supports continuous operation in mission-critical medical systems
Best Practices
- Select power supplies pre-certified to IEC 60601‑1 and IEC 60601‑1-2
- Conduct worst-case leakage and EMI testing at the system level
- Avoid general-purpose PSUs unless third-party medical certification is provided
Meeting these electrical safety benchmarks is the price of admission for any power supply intended for medical use.
How Do Isolation and Leakage Current Requirements Affect Power Supply Design?
In medical applications, power supply isolation isn’t just about noise reduction—it’s about life safety. Isolation and leakage current standards under IEC 60601‑1 exist to protect patients, especially those connected via sensors, probes, or implanted leads. These systems must isolate the patient from any risk of electrical shock, even during fault conditions.
To meet these criteria, power supply design must include:
- Galvanic isolation between input and output
- Creepage and clearance distances based on altitude and pollution degree
- Leakage current suppression via specialized input filters and transformer design
OEMs must also ensure that the power supply does not allow fault conditions to propagate, even if a component fails. For applications classified as BF (body floating) or CF (cardiac floating), the standards are even stricter, often requiring <10 µA of leakage.
Top Features
- Reinforced isolation barriers between primary and secondary circuits
- Medical-grade filtering and shielded designs
- Isolated signal and control interfaces to prevent ground loops
Top Benefits
- Guarantees safe operation in direct-contact or invasive devices
- Supports global compliance, including FDA and EU MDR requirements
- Reduces engineering burden for end-product IEC 60601‑1 certification
Best Practices
- Choose power modules with certified 2 x MOPP isolation
- Verify leakage current across varying line conditions and grounding scenarios
- Ensure proper PCB layout spacing and track width to maintain insulation ratings
Designing for medical isolation isn’t just about passing tests—it’s about building confidence into every connection.
CLIENT'S QUOTE
"Phihong’s PoE solutions have made a huge difference for us! Our network runs more efficiently, and we’ve seen real cost savings. We couldn’t be happier!"
How to Manage EMI and EMC in Medical Power Supply Design
EMI (electromagnetic interference) and EMC (electromagnetic compatibility) play a critical role in medical power supply design under IEC 60601‑1-2, the collateral standard specifically addressing electromagnetic safety. In medical environments—where devices like ventilators, monitors, and infusion pumps operate side by side—EMI control isn’t just best practice; it’s mandatory.
Medical power supplies must be designed to avoid both radiated and conducted interference. They must also remain immune to external EMI from nearby devices, hospital equipment, or wireless networks. Poor EMI design can result in false readings, device resets, or even full operational failure.
Top Features
- Low-noise switching topologies and shielded designs
- Built-in EMI filters (Class B or better) for conducted emissions
- Surge and ESD protection circuits to handle hospital-grade test pulses
Top Benefits
- Ensures device accuracy in critical care and diagnostic applications
- Meets global EMI emission and immunity standards (EN, FCC, CISPR)
- Reduces test lab failures and certification delays
Best Practices
- Use medical-grade EMI filters integrated into the power module
- Perform pre-compliance EMC testing early in development
- Incorporate ferrite beads, chokes, and ground planes in PCB design
Controlling EMI/EMC is essential for patient safety and clinical accuracy—every OEM needs to engineer for it, not just test for it.
What Documentation and Testing Are Required to Achieve IEC 60601‑1 Certification?
IEC 60601‑1 compliance goes beyond hardware—it requires extensive documentation, traceability, and third-party testing. OEMs must provide a complete technical file that demonstrates conformity with each safety requirement, including risk assessments and validation reports.
A successful certification process involves:
- Pre-compliance evaluations to identify design risks early
- Safety-critical component traceability (e.g., transformers, capacitors, optoisolators)
- Environmental and mechanical testing (vibration, drop, ingress, etc.)
- Documentation of MOOP/MOPP distances, dielectric tests, and leakage measurements
Once the design is finalized, OEMs must submit prototypes to certified test labs (such as UL, TÜV, or Intertek) for formal evaluation. The lab will test the device under worst-case load, environmental conditions, and fault scenarios to ensure full IEC 60601‑1 adherence.
Top Features
- Test reports covering dielectric strength, touch current, and temperature rise
- Bill of Materials (BOM) with approved component references
- Design history file (DHF) and risk management file (RMF) aligned with ISO 14971
Top Benefits
- Faster regulatory clearance and global market entry
- Reduced risk of audit findings or product recalls
- Builds trust with hospital purchasers and medical device integrators
Best Practices
- Work with power supply vendors that provide pre-certified modules
- Develop a compliance roadmap that includes lab scheduling and buffer time
- Maintain digital records of every design iteration, test result, and risk control
Compliance is a system-wide effort—documentation and discipline are as important as the design itself.
How Phihong USA Helps OEMs Manufacture IEC 60601‑1 Compliant Medical Power Supplies
Phihong USA is a trusted partner for OEMs in the medical device industry, offering certified, high-reliability power solutions engineered to meet the stringent demands of IEC 60601‑1. Whether you’re designing a Class II diagnostic device, a surgical support system, or a patient-connected monitor, Phihong’s medical-grade power supplies deliver the safety, performance, and documentation required for global compliance.
Phihong offers:
- IEC 60601‑1 certified external and embedded power supplies
- 2 x MOPP isolation, low-leakage current, and EMI-optimized designs
- Pre-compliance testing and regulatory documentation support
- Custom power design for specialized form factors or unique operating environments
- ISO 13485 manufacturing processes and traceable production quality
Backed by global supply chain capabilities and decades of expertise in power electronics, Phihong supports every phase of your medical product development—from prototyping and safety reviews to production and post-market support.
If you’re looking for a power supply partner who understands the critical nature of medical compliance, Phihong USA is here to help.
Start your project at www.phihong.com or contact usasales@phihongusa.com for a consultation.
Contact Our Team Today!
Our dedicated sales team and international partners are prepared to support you with your latest projects and initiatives globally.
Explore More with Phihong USA
As we conclude our exploration of PoE technology, it’s evident how these innovations are streamlining power and data integration across various industries. Phihong USA stands at the forefront of this technological advancement, offering a diverse range of power solutions designed to meet the evolving needs of modern industries.
Phihong USA’s extensive product lineup includes:
- Power over Ethernet (PoE) Solutions: Delivering reliable power and data transmission over a single cable, ideal for simplifying network installations and reducing costs.
- AC/DC Adapters and Power Supplies: From compact adapters to industrial-grade power supplies, Phihong provides solutions that ensure efficiency and reliability in various applications.
- Battery Chargers: Customizable chargers for lithium-ion and lead-acid batteries, supporting a wide range of power requirements for mobility and industrial applications.
- Medical Power Supplies: Specialized power solutions designed to meet the stringent requirements of the healthcare industry, ensuring safety and reliability.
Phihong USA is committed to innovation and excellence, continually developing products that meet the highest standards of performance and reliability. Their global reach and dedication to customer support make them a trusted partner in powering the future.
Here are some useful links to explore Phihong USA’s offerings further and bring in new potential clients:
Visit Phihong USA to discover how their advanced power solutions can support your business needs. Whether you’re looking to upgrade your network, or find reliable power supplies, Phihong USA has you covered.
By choosing Phihong USA, you’re partnering with a leader in power technology, ensuring your operations run smoothly and efficiently with top-tier power solutions. Contact Us today!
FAQ
What is the difference between MOOP and MOPP in IEC 60601‑1?
MOOP (Means of Operator Protection) and MOPP (Means of Patient Protection) are two safety designations defined in IEC 60601‑1 that specify the level of insulation, clearance, creepage, and test voltage required to protect users from electrical hazards. The key difference lies in risk exposure—MOPP requirements are more stringent because they are intended for devices that may have direct or indirect contact with patients.
- 1 x MOOP is acceptable for devices only handled by trained operators (e.g., lab equipment).
- 2 x MOPP is required for devices that come into physical contact with patients or are used in clinical settings (e.g., infusion pumps, ECG machines).
For power supply manufacturers, this distinction impacts transformer design, insulation thickness, dielectric strength, and even spacing on printed circuit boards. Using a 2 x MOPP-certified power module ensures the supply meets the highest level of protection, reducing design risk and simplifying regulatory approval for medical device OEMs. In general, OEMs should opt for 2 x MOPP supplies to ensure broader compliance across global markets.
Why is leakage current so important in medical power supplies?
Leakage current refers to unintended electrical current that escapes from the power supply’s circuit and flows to the ground—or, in worst cases, to the patient or operator. In medical applications, even small levels of leakage can pose serious safety risks, particularly when devices are used on vulnerable or critically ill patients.
IEC 60601‑1 places strict limits on leakage current:
- Patient leakage current must typically be less than 100 µA, and in some cardiac (CF) applications, below 10 µA.
- Touch current for operators must also be minimized, with redundant protections built in to detect and stop abnormal current flow.
OEMs must carefully select power supplies that use medical-grade isolation, effective filtering, and proper grounding to keep leakage within safe levels. High-quality supplies also include protective circuits that isolate faults and prevent leakage from escalating.
Measuring and documenting leakage current under worst-case conditions is essential for IEC 60601‑1 certification and for building equipment that clinicians and healthcare providers can trust.
What types of medical devices require IEC 60601‑1 compliant power supplies?
Any electrical medical equipment intended to diagnose, treat, or monitor patients must meet IEC 60601‑1 compliance, which includes having a certified power supply. This applies to both clinical and home-use devices, such as:
- Patient monitors and imaging equipment
- Infusion pumps and dialysis machines
- Surgical and electrosurgical systems
- Diagnostic and laboratory instruments
- Home-use medical electronics (e.g., CPAP, nebulizers)
Whether the device is used in a hospital, ambulance, or patient home, the power supply must ensure safe operation under all conditions. IEC 60601‑1 certified power supplies guarantee isolation, leakage protection, EMI performance, and fire resistance—making them essential for legal and commercial approval.
OEMs targeting global markets must ensure their power supplies meet these criteria to satisfy not only IEC standards, but also FDA, CE, and other local regulatory requirements.
Can general-purpose power supplies be used in medical devices?
Technically, yes—but only under certain conditions, and it’s rarely advisable. General-purpose power supplies may meet basic safety requirements like UL 60950 or EN 62368, but they typically do not meet the stricter insulation, leakage, and EMC standards set by IEC 60601‑1.
Using non-medical PSUs in medical equipment introduces several risks:
- Failing pre-compliance EMI or leakage current testing
- Failing to achieve global certification
- Risking patient safety and legal liability in case of failure
Additionally, using uncertified supplies can delay product approval, complicate audits, or result in mandatory redesigns. Most OEMs find it more efficient—and safer—to use pre-certified IEC 60601‑1 power supplies from the start.
Medical-grade PSUs are specifically engineered with 2 x MOPP isolation, low leakage, and EMC resilience, reducing risk and speeding time to market. For any equipment classified as a medical device, using a general-purpose PSU is almost never worth the trade-off.
How does Phihong USA help OEMs meet IEC 60601‑1 requirements?
Phihong USA provides medical OEMs with a wide range of IEC 60601‑1 compliant power solutions that simplify regulatory approval and accelerate time-to-market. We support both standard and custom power supply designs for clinical, diagnostic, and home medical applications.
Here’s how we help:
- Certified 2 x MOPP power modules with ultra-low leakage current
- EMC-optimized layouts tested to meet IEC 60601‑1-2
- Support for documentation, test data, and pre-compliance review
- Thermal and mechanical customization for unique enclosure requirements
- ISO 13485 manufacturing standards for traceable, repeatable production quality
Whether you’re developing a Class I or Class II medical device, Phihong’s engineering team will help you navigate every phase of certification—from prototype to test lab to commercial launch.
Contact us at sales@phihongusa.com or visit www.phihong.com to learn how our medical-grade power supplies can accelerate your next product.